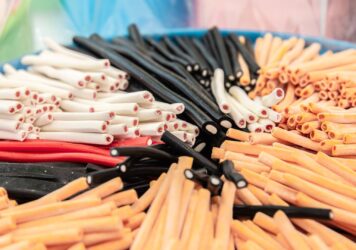
What is Custom Plastic Extrusion?
Custom plastic extrusion is a process that creates plastic products specified to almost any shape and size. The extrusion process is used for a wide variety of applications across various industries due to its versatility and ability to produce custom shapes and dimensions.
What is Custom Plastic Extrusion Used For?
Custom plastic extrusion is a versatile manufacturing process that caters to a wide range of industries and applications. The process offers flexibility in design, material selection, and production scalability. Some of the most popular uses include:
Pipes & Tubes
Custom plastic extrusion is extensively used in the manufacturing of pipes and tubing for applications such as plumbing, irrigation, drainage, and conduits for electrical wiring.
Profile Extrusions
Extruded plastic profiles are used in construction for applications such as window and door frames, trim, and decorative edging. They’re also used in automotive applications for sealing, trim, and body components.
Cable & Wire Coatings/Jackets
Extruded plastic is used to provide insulation and protection for electrical wires and cables in a wide range of applications.
Custom Plastic Components
Extrusion allows for the production of custom-designed components used in industries such as aerospace, electronics, appliances, and consumer goods.
How Does Custom Plastic Extrusion Work?
During the extrusion process, the thermoplastic material is melted and forced through a die, which is a tool with a specific shape, to produce continuous lengths of the desired cross-sectional profile. The extruded plastic is then cooled and solidified to form the final product.
Custom plastic extrusion allows for producing a wide range of products, including pipes, tubing, rods, profiles, and various other components used in industries such as construction, automotive, electronics, and consumer goods.
The process can be tailored to meet the specific requirements of a particular application, including the choice of materials, dimensions, and tolerances. This flexibility makes custom plastic extrusion suitable for both large-scale production runs and specialized projects where unique shapes or properties are needed.
Environmentally Friendly Closed-Loop Water Cooling System
Striving to be as environmentally friendly as possible should be a top priority for any major custom extrusion manufacturer. A huge part of this is using an environmentally friendly closed-loop water cooling system. What does this mean?
An environmentally friendly closed-loop water cooling system is a type of cooling system designed to minimize water consumption, reduce energy usage, and mitigate environmental impact. Unlike open-loop systems that continuously draw water from external sources and release it back into the environment, closed-loop systems circulate a fixed volume of water within a closed system, reducing water consumption and preventing contamination of natural water sources.
Water contamination from plastics has become a huge issue in recent years. Closed-loop cooling systems help prevent plastics from entering the environment via open loops and common water systems.
Custom Extrusion with Inplex
Looking for quality custom extrusion products and services? Inplex is one of the leading custom extrusion services in the US, with over 50 years of experience. We pride ourselves on our ability to put the right talent and technology in place to perform the best possible job for our clients.
We own a 42,000 sq. ft. facility in Naperville, Illinois, that is temperature-controlled and features an environmentally friendly closed-loop water cooling system. If you have specific needs or questions, don’t hesitate to contact us!
Back to Blog