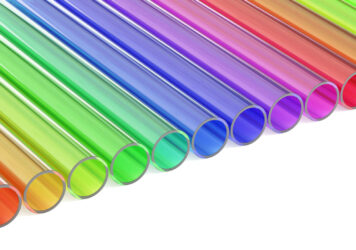
What is a Custom Profile Extrusion?
Custom plastic profile extrusion is a manufacturing process used to create plastic profiles with unique shapes, dimensions, and features according to specific design requirements. During custom profile extrusion, thermoplastic materials are melted and formed into continuous profiles by forcing them through a die or series of dies. The resulting plastic profiles can have a wide range of cross-sectional shapes, including complex geometries, and can be produced in various lengths.
Custom plastic profile extrusion is a versatile and efficient manufacturing process for producing custom-designed plastic profiles tailored to meet almost any need. How does the process work? By following a few specific steps.
Material Selection
The process begins with the selection of thermoplastic materials suitable for the intended application. Common materials used in profile extrusion include many different types of composite materials. The material choice depends on factors such as mechanical properties, chemical resistance, temperature resistance, and desired appearance.
Melting & Mixing
The selected thermoplastic material is fed into an extruder, where it is heated and melted to a controlled temperature. During this stage, additives such as colorants, stabilizers, or reinforcing agents may be introduced to modify the properties of the plastic.
Extrusion
The molten plastic material is then forced through a shaped die or series of dies, which impart the desired cross-sectional shape to the extruded profile. The die(s) are custom-designed to produce profiles with specific dimensions, features, and surface finishes. The extrusion process may involve single or multiple stages, depending on the complexity of the profile.
Cooling & Sizing
After exiting the die, the extruded profile is rapidly cooled using water or air to solidify the plastic material. Cooling ensures that the profile retains its shape and dimensions. Sizing tools or calibration equipment may be used to maintain precise dimensions and tolerances.
Cutting & Finishing
Once the extruded profile has cooled and solidified, it is cut to the desired length using saws or guillotine cutters. Additional finishing operations, such as punching, notching, drilling, or machining, may be performed to add features or prepare the profile for assembly.
Quality Controls
Throughout the extrusion process, quality control measures are implemented to ensure that the final profiles meet the required specifications and standards. This may include monitoring parameters such as temperature, pressure, dimensions, surface finish, and mechanical properties.
Custom Extrusion with Inplex
Looking for quality custom extrusion products and services? Inplex is one of the leading custom extrusion services in the US, with over 50 years of experience. We pride ourselves on our ability to put the right talent and technology in place to perform the best possible job for our clients.
We own a 42,000 sq. ft. facility in Naperville, Illinois, that is temperature-controlled and features an environmentally friendly closed-loop water cooling system. If you have specific needs or questions, don’t hesitate to contact us!
Back to Blog