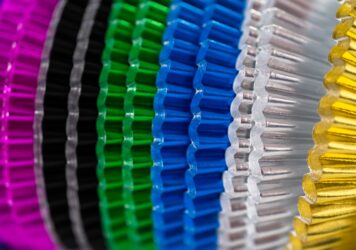
Understanding Tolerances in Plastic Extrusion: What You Need to Know
Understanding tolerances in plastic extrusion is key to balancing quality, performance, and cost. By carefully considering material properties, design complexity, and manufacturing capabilities, you can set realistic tolerances that meet application needs while maintaining efficiency.
Tolerances in plastic extrusion are critical parameters that define the allowable deviation from specified dimensions or properties of the extruded product. Understanding tolerances is essential for ensuring the quality, functionality, and compatibility of the final product.
Let’s take a quick look at what everyone should know about tolerances in plastic extrusion.
What is Tolerance
Tolerances refer to the permissible variation in dimensions or other specifications (e.g., thickness, shape, or material properties) during the extrusion process. These variations are typically expressed as plus or minus values (ie ±0.02 inches etc).
Factors Influencing Tolerances
Several factors can impact the achievable tolerances in plastic extrusion:
Material Properties
- Different plastics (e.g., PVC, polyethylene, polycarbonate) have unique thermal and mechanical properties that affect tolerances.
- Plastics with high thermal expansion rates may exhibit greater dimensional variation.
Profile Complexity
- Simple profiles (e.g., tubes or flat sheets) generally allow for tighter tolerances.
- Complex shapes with intricate features may require looser tolerances due to challenges in consistent shaping.
Die Design
- The precision of the custom extrusion die significantly influences the dimensional accuracy.
- Well-designed dies minimize variations and maintain consistent product quality.
Extrusion Process Conditions
- Temperature, pressure, and cooling rates directly affect material flow and stability.
- Variations in these parameters can lead to deviations in dimensions.
Post-Processing
- Cutting, trimming, or other finishing operations may introduce additional variations, impacting tolerances.
Types of Tolerances
Dimensional Tolerances
Specify the acceptable range for physical dimensions like width, height, and wall thickness.
Shape Tolerances
Define the permissible variation in the profile’s shape, ensuring the product maintains its intended geometry.
Material Tolerances
Address variations in material properties, such as hardness, flexibility, or UV resistance.
Importance of Tolerances
Functionality
Ensures the extruded part fits and functions as intended in its application.
Interchangeability
Allows parts to be interchangeable with other components, especially in assembly applications.
Cost-Effectiveness
Tight tolerances can increase production costs, so setting realistic tolerances balances quality and expense.
Regulatory Compliance
Some industries (e.g., medical or aerospace) require strict adherence to specified tolerances for safety and reliability.
Practical Tolerance Tips
- Avoid over-specifying tolerances unnecessarily, as this can increase costs without adding value.
- Work with experienced extrusion manufacturers who understand the material and process limitations.
- Perform prototypes and test runs to validate tolerances before full-scale production.
Custom Extrusion with Inplex
Looking for quality custom extrusion products and services? Inplex is one of the leading custom extrusion services in the US, with over 50 years of experience. We pride ourselves on our ability to put the right talent and technology in place to perform the best possible job for our clients.
We own a 42,000 sq. ft. facility in Naperville, Illinois, that is temperature-controlled and features an environmentally friendly closed-loop water cooling system. If you have specific needs or questions, don’t hesitate to contact us!
Back to Blog