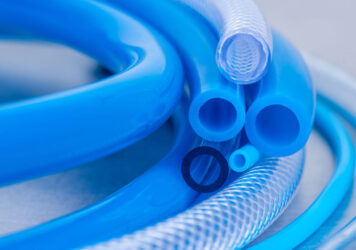
The Role of Custom Plastic Tubing in the Automotive Industry
The automotive industry is constantly evolving, with manufacturers pushing the limits of technology, sustainability, and safety. One of the often-overlooked but crucial components that contribute to the efficiency and performance of vehicles is custom plastic tubing.
These specialized tubes are tailored to meet the exact specifications required for various automotive applications, from fluid management systems to air intake systems. Custom plastic tubing plays a vital role in enhancing vehicle performance, durability, and overall functionality.
Let’s take a closer look at the role of custom plastic tubing in the automotive industry.
Advantages of Custom Plastic Tubing
Custom plastic tubing offers several benefits over traditional metal or rubber alternatives. One of the key advantages is its lightweight nature. Reducing vehicle weight is a priority in modern automotive design, as lighter vehicles improve fuel efficiency and reduce carbon emissions. Plastic tubing helps achieve these goals by replacing heavier metal pipes, contributing to overall vehicle weight reduction.
Plastic tubing also offers superior resistance to corrosion compared to metal alternatives. Automotive systems often encounter moisture, chemicals, and extreme temperatures, which can cause metal tubes to rust or degrade over time.
Custom plastic tubes are resistant to these environmental factors, ensuring that automotive systems remain functional for longer periods, even under harsh conditions. This corrosion resistance is particularly important in applications such as fluid transport systems, where exposure to brake fluid, coolant, or other chemicals is common.
Moreover, custom plastic tubing can be engineered for specific applications, allowing for greater flexibility in design and installation. Whether the need is for flexibility in routing around tight spaces or high-pressure resistance, plastic tubing can be tailored to meet these demands. Its adaptability allows for improved system integration, contributing to more efficient and compact designs.
Applications in the Automotive Industry
Custom plastic tubing is utilized in a variety of automotive systems, where its properties can provide unique solutions. One of the primary uses is in fluid transport systems. These include brake lines, fuel lines, coolant systems, and power steering systems. Plastic tubing is ideal for these applications because of its lightweight nature and resistance to corrosion, which ensures long-lasting and reliable fluid flow.
In addition, plastic tubing is extensively used in air intake systems. Modern vehicles often feature sophisticated air intake systems designed to improve engine efficiency and reduce emissions.
Custom plastic tubing is used to route air from the intake manifold to the engine, ensuring the proper airflow necessary for optimal combustion. The lightweight and durable nature of plastic tubing in these applications helps reduce the overall weight of the air intake system while maintaining performance and reliability.
Another important application is in HVAC (heating, ventilation, and air conditioning) systems. Custom plastic tubing is used to transport refrigerants and air within the vehicle’s HVAC system. Plastic’s resistance to extreme temperatures makes it an ideal material for these systems, which need to function effectively even in extreme weather conditions. Additionally, the flexibility of custom plastic tubing allows for easy routing within the complex and space-constrained interiors of modern vehicles.
The Future of Custom Plastic Tubing in Automotive Design
As the automotive industry shifts towards electric vehicles (EVs) and more environmentally conscious designs, the demand for custom plastic tubing is expected to grow. With EVs becoming more mainstream, systems like battery cooling and high-voltage cable insulation will require specialized plastic tubing to meet the unique demands of electric drivetrains.
Furthermore, as vehicles become more integrated with smart technologies and automated systems, custom plastic tubing will continue to play a critical role in supporting complex fluid and air transport systems.
In addition to performance improvements, manufacturers are focusing on the sustainability of automotive components. Custom plastic tubing is increasingly being produced with recyclable and eco-friendly materials, further reducing the environmental impact of automotive manufacturing.
Custom Extrusion with Inplex
Looking for quality custom extrusion products and services? Inplex is one of the leading custom extrusion services in the US, with over 50 years of experience. We pride ourselves on our ability to put the right talent and technology in place to perform the best possible job for our clients.
We own a 42,000 sq. ft. facility in Naperville, Illinois, that is temperature-controlled and features an environmentally friendly closed-loop water cooling system. If you have specific needs or questions, don’t hesitate to contact us!
Back to Blog