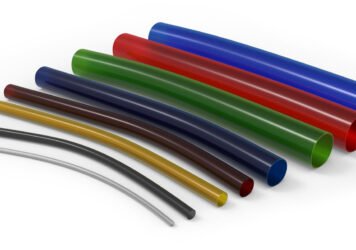
The Difference Between Plastic Coating & Plastic Jacketing
Plastic coating and plastic jacketing are two different methods of applying a protective layer of plastic to a substrate, like metal wire or tubing. While coating & jacketing serve similar purposes, there are differences in their application techniques, the materials used, and the level of protection they offer.
Each method has its advantages and is chosen based on specific requirements, including desired protection level, environmental conditions, and manufacturing considerations. Let’s take a look at the differences.
Application Technique
Plastic coating typically involves dipping or spraying the substrate with a liquid plastic material, such as PVC (Polyvinyl Chloride) or polyethylene, and then curing or drying the coating to form a solid protective layer. The coating adheres directly to the surface of the substrate.
Plastic jacketing involves extruding a hollow plastic tube or sleeve around the substrate, and encapsulating it within the plastic material. The substrate is inserted into the jacketing material, and the jacket is formed around it using heat and pressure.
Materials
Plastic coatings are often made from thermoplastic materials, such as PVC, polyethylene, or nylon, which can be applied in liquid form and then solidify upon curing. These materials provide a durable, protective barrier against corrosion, abrasion, and chemical exposure.
Plastic jackets are typically made from thermoplastic or thermosetting materials, such as PVC, polyethylene, polypropylene, or TPE (Thermoplastic Elastomer). These materials are extruded into the desired shape and can offer varying degrees of flexibility, impact resistance, and environmental resistance.
Protection
Plastic coatings provide a thin, uniform layer of protection directly applied to the surface of the substrate. They offer good corrosion resistance, abrasion resistance, and electrical insulation properties. However, they may be susceptible to damage if the coating is compromised or worn away.
Plastic jackets provide a thicker, more robust layer of protection that completely encases the substrate. They offer superior protection against mechanical damage, environmental exposure, and harsh conditions. Plastic jackets are commonly used in applications where the substrate needs to withstand heavy-duty use, extreme temperatures, or outdoor environments.
Flexibility
Plastic coatings can be applied to substrates of various shapes, sizes, and configurations using dipping, spraying, or painting methods. They are suitable for coating wires, cables, pipes, and other irregularly shaped objects.
Plastic jackets are typically extruded in continuous lengths and then cut to size for specific applications. They are well-suited for encapsulating long lengths of wire, cable, tubing, or structural components.
Custom Extrusion with Inplex
Looking for quality custom extrusion products and services? Inplex is one of the leading custom extrusion services in the US, with over 50 years of experience. We pride ourselves on our ability to put the right talent and technology in place to perform the best possible job for our clients.
We own a 42,000 sq. ft. facility in Naperville, Illinois, that is temperature-controlled and features an environmentally friendly closed-loop water cooling system. If you have specific needs or questions, don’t hesitate to contact us!
Back to Blog