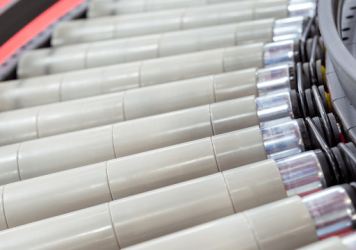
The Custom Plastic Extrusion Process Explained
Custom plastic extrusion allows for high precision and flexibility in producing a wide range of products with consistent quality and performance. The process involves several key steps to transform raw plastic material into finished products with specific shapes and dimensions.
Let’s take a closer look at how the custom plastic extrusion process works in laymen’s terms.
Material Preparation
- Resin Selection. The process begins with selecting the appropriate plastic resin or polymer, such as PVC, polyethylene, or polypropylene, based on the desired properties of the final product.
- Compounding. The resin is often mixed with additives, colorants, or fillers to achieve specific characteristics like flexibility, strength, or color.
Feeding
The prepared resin is fed into a hopper, which delivers it into the extruder. The hopper ensures a steady and consistent flow of material.
Melting & Mixing
- Extruder. The resin is conveyed through a heated barrel in the extruder, where it is subjected to controlled temperatures to melt it into a homogeneous, molten state.
- Mechanism. Inside the barrel, a rotating screw or auger pushes the molten plastic forward and mixes it to ensure uniformity.
Shaping
- Die Formation. The molten plastic exits the extruder through a die, which shapes it into the desired cross-sectional profile. The die can be custom-designed to produce specific shapes such as tubes, profiles, or sheets.
- Cooling. As the extruded plastic exits the die, it is rapidly cooled to solidify its shape. Cooling methods can include air cooling, water baths, or a combination of both.
Cutting & Finishing
- Cutting. Once the plastic has cooled and solidified, it is cut into the desired lengths or shapes. This can be done using various cutting tools, such as saws or blades.
- Finishing. The finished extruded product may undergo additional finishing processes, such as trimming, drilling, or surface treatment, to meet specific requirements or improve appearance.
Quality Control
Throughout the process, quality control checks are performed to ensure the extruded products meet the required specifications for dimensions, strength, and surface finish.
Packaging & Shipping
The final products are packaged and prepared for shipment. Packaging may include wrapping, bundling, or labeling to protect the products during transit and provide necessary information.
Custom Extrusion with Inplex
Looking for quality custom extrusion products and services? Inplex is one of the leading custom extrusion services in the US, with over 50 years of experience. We pride ourselves on our ability to put the right talent and technology in place to perform the best possible job for our clients.
We own a 42,000 sq. ft. facility in Naperville, Illinois, that is temperature-controlled and features an environmentally friendly closed-loop water cooling system. If you have specific needs or questions, don’t hesitate to contact us!
Back to Blog