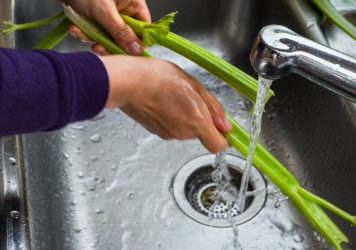
Rigid vs. Flexible Vinyl
Polyvinyl Chloride (PVC or Vinyl) is an economical and versatile thermoplastic polymer widely used in the plumbing and construction industry to produce custom profiles, pipes (drinking and wastewater), wire and cable insulation, medical devices, etc. Commonly regarded as one of the most versatile and cost-effective materials, due to its versatile properties, and easy processability. PVC can be made very soft through the extrusion process with the use of a plasticizer or other additive.
Polyvinyl Chloride is available in two broad categories: Flexible and Rigid.
RPVC [Rigid Polyvinyl Chloride]
Unsurprisingly, rigid vinyl (RPVC) finds its most effective use when rigidity is particularly desired. RPVC combines excellent resistance properties to water and chemicals with affordability, making it a popular choice in tubing and profiles. However, given that PVC contains chemical additives like lead and cadmium, it must be ordered at FDA grade to be safe to use for applications involving drinking water. As the name suggests, rigid polyvinyl chloride (RPVC) boasts superior rigidity. Priced moderately and manufactured by using raw materials like rock salt and natural gas, rigid vinyl offers excellent resistance to weathering and water, although RPVC should be heat-stabilized to deal with high temperatures. The material can also be UV stabilized through the use of additives, which offers increased resistance to sunlight. By definition, rigid vinyl has not been modified through the use of plasticizers, which are sometimes applied to make the vinyl softer and more flexible. Rigid vinyl is susceptible to strong solvents, including esters and hydrocarbons. RPVC is used most commonly in plumbing and the construction industry in general.
Plumbing pipes are perhaps the most recognizable application of RPVC material, leading to rigid vinyl’s popularity in the construction and plumbing industries. RPVC’s water resistance makes it suitable for uses in windows, doorways, wire coverings, and wastewater pipes. Rigid PVC can also be used to create plastic film and can take be matte, opaque, or glossy. It is available in clear or colored varieties and can it can be extruded into many different colors and offers versatility for outdoor projects. RPVC can be ordered in either FDA or outdoor grades.
FPVC [Flexible Polyvinyl Chloride]
On the flipside of RPVC comes flexible polyvinyl chloride (FPVC). Flexible vinyl is versatile and has usually been modified from its rigid variant through the addition of plasticizer or another additive. FPVC is often used for plastic packaging and can be modified into unusual shapes, like jar lids. FPVC is especially useful for plastic packaging, as its flexibility allows it to be formed into unconventional shapes. It can also be ordered according to FDA standards for applications involving food or drinking water. It has also found use in home construction, especially in flooring, roofing, and wall covering. FPVC is noted for the wide range of substances that it is able to carry, including a wide range of chemicals, liquids, and gasses.
As a recyclable thermoplastic, flexible vinyl also provides exceptional environmental performance. Due to its strong insulation properties and abrasion resistance, flexible PVC is commonly used for plastic profile extrusion. FPVC material is available in varying degrees of toughness, from its default flexibility to semi-rigid variants. FPVC can be UV stabilized and offers excellent heating resistance. Flexible vinyl comes in a variety of clear or opaque colors, the latter of which work best for outdoor applications. While FPVC has been noted for being able to serve as packaging material to carry a wide range of substances.
Rigid Polyvinyl Chloride vs. Flexible Polyvinyl Chloride
Both rigid vinyl and flexible vinyl are extremely affordable and cost-effective. Contrary to RPVC’s notable rigidity, FPVC is soft and suited for applications that require flexibility above and beyond what rigid vinyl is able to provide. FPVC can easily be shaped and arranged to serve your needs. Flexible vinyl does not rust or corrode and is lightweight and easy to work with, relative to other materials. The flexibility inherent in FPVC comes with a drawback in that it is not able to tolerate as much pressure as rigid vinyl (RPVC) and is more prone to kinking at lower densities. Flexible vinyl, at least relative to rigid vinyl, is its limited capacity for tolerating pressure beyond a certain point. FPVC material is more prone to kinking, depending upon how thin it is. Furthermore, unless it is ordered according to FDA-approved grades, tubing made from rigid vinyl is not safe for drinking water. This is because PVC can contain chemical additives like lead, cadmium, and phthalates. FPVC can also be ordered according to FDA standards combined with its flexibility makes it ideal for applications involving food or drinking water. While rigid vinyl’s combination of rigidity, all-around utility, and affordability makes it a good choice for tubes or profiles.
At Inplex, we will deliver a product that exceeds your expectations! We work closely with each and every client to understand their needs and we use that knowledge to hand-select the right materials and preparation techniques.
Back to Blog