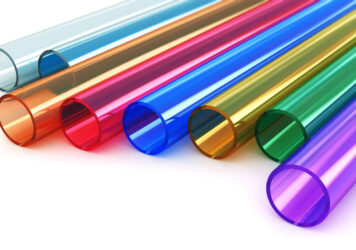
Reducing Production Costs with Custom Plastic Extrusion Solutions
Cost reduction in custom plastic extrusion involves a balance of thoughtful design, efficient production practices, and strategic material choices. Collaborating with experienced manufacturers and continually optimizing processes will help achieve cost-effective solutions without compromising product quality.
Reducing production costs in custom plastic extrusion projects requires strategic planning, efficient processes, and thoughtful design choices. Let’s take a closer look at how costs can be reduced.
Optimize Design for Manufacturability
Simplify Profiles
- Minimize intricate shapes, sharp corners, or unnecessary complexity in the design.
- Uniform wall thickness reduces material usage and prevents manufacturing issues.
Incorporate Standard Features
Use commonly available features and materials that require less custom tooling.
Adjust Tolerances
Avoid over-specifying tight tolerances unless necessary, as they increase production difficulty and costs.
Cost-Effective Materials
Select Suitable Plastics
Choose materials that meet performance needs without being over-engineered. For example, use PVC instead of polycarbonate for non-load-bearing applications.
Leverage Material Alternatives
Explore blended or recycled plastics for lower costs, provided they meet quality standards.
Reduce Additive Usage
Limit expensive additives (e.g., UV inhibitors, colorants) to only essential levels.
Efficient Tooling
High-Quality Dies
Invest in durable and precision-engineered dies to ensure consistency and minimize downtime for repairs.
Multi-Cavity Tooling
For high-volume production, multi-cavity dies can extrude multiple profiles simultaneously, increasing output and reducing per-unit costs.
Streamline the Extrusion Process
Optimize Production Parameters
Adjust temperature, pressure, and speed to ensure efficient extrusion without material waste or defects.
Minimize Setup Time
Use quick-change systems for dies and tooling to reduce machine downtime between production runs.
Automate Processes
Implement automation for material feeding, cooling, and cutting to reduce labor costs and improve consistency.
Reduce Waste & Scrap
Material Recycling
Collect and reprocess scrap material to reuse in production when feasible.
Consistent Quality Checks
Monitor production closely to detect issues early and reduce waste caused by defective parts.
Precision in Cutting
Use accurate cutting tools to minimize off-cuts and ensure consistent product length.
Partner with an Experienced Manufacturer
Expertise
Work with a manufacturer experienced in optimizing extrusion processes and materials for cost efficiency.
Specialized Operations
Delegate post-processing or specialized tasks (e.g., co-extrusion, finishing) to reduce specialized or unusual in-house costs.
Energy Efficiency
Up-to-Date Equipment
Use modern, energy-efficient extrusion machines that reduce electricity usage.
Process Optimization
Run machines at optimal speeds to balance energy consumption with output efficiency.
Custom Extrusion with Inplex
Looking for quality custom extrusion products and services? Inplex is one of the leading custom extrusion services in the US, with over 50 years of experience. We pride ourselves on our ability to put the right talent and technology in place to perform the best possible job for our clients.
We own a 42,000 sq. ft. facility in Naperville, Illinois, that is temperature-controlled and features an environmentally friendly closed-loop water cooling system. If you have specific needs or questions, don’t hesitate to contact us!
Back to Blog