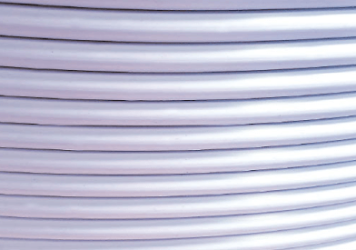
Plastic Extrusion Solutions for the Automotive Industry: Meeting High Standards
Plastic extrusion companies meet the high standards of the automotive industry by leveraging advanced materials, precision manufacturing, and stringent quality control. Their ability to deliver customized, high-performance components while aligning with sustainability goals ensures their integral role in the evolution of automotive design and technology.
Plastic extrusion companies play a critical role in meeting the stringent standards of the automotive industry, which demands precision, durability, and performance in every component. Let’s take a look at how.
Utilizing High-Performance Materials
Advanced Polymers. Plastic extrusion companies use materials like polycarbonate, ABS, polypropylene, and thermoplastic elastomers (TPEs) to meet the specific needs of the automotive sector.
Heat and Chemical Resistance. Materials are selected and engineered to withstand high temperatures, fuel exposure, and harsh environmental conditions.
Lightweighting Solutions. Extruded plastic components replace heavier metal parts, improving fuel efficiency and reducing emissions.
Precision Manufacturing Processes
Tight Tolerances. Advanced extrusion technology ensures parts are manufactured to precise dimensions, critical for fit and function in automotive applications.
Multi-Layer Extrusion. Co-extrusion techniques produce components with multiple layers, providing enhanced functionality such as insulation, impact resistance, or UV protection.
Quality Consistency. Modern equipment and automated controls maintain consistency across high-volume production runs.
Customization and Design Flexibility
Complex Profiles. Plastic extrusion can create intricate shapes and designs tailored to specific automotive requirements, such as weatherstripping, seals, and interior trims.
Aesthetic Features. Custom colors, textures, and finishes ensure parts align with the vehicle’s overall design and branding.
Integration of Functional Additives. Companies incorporate additives for fire resistance, anti-static properties, or enhanced durability.
Compliance with Automotive Standards
ISO/TS Certifications. Many plastic extrusion companies adhere to international standards and other certifications specific to automotive quality management.
Testing and Validation. Components undergo rigorous testing for tensile strength, impact resistance, heat aging, and chemical compatibility to meet OEM and regulatory requirements.
Advanced Technologies
Smart Manufacturing. Integration of IoT and AI for real-time monitoring and predictive maintenance ensures high-quality production.
Prototyping with 3D Printing. Rapid prototyping capabilities allow for quick development and testing of new designs, reducing time-to-market.
Digital Twins. Virtual modeling of the extrusion process ensures optimal production parameters for each component.
Scalability and High-Volume Production
Streamlined Operations. Extrusion companies invest in equipment and processes that allow for efficient production of large quantities without compromising quality.
Inventory Management. Advanced logistics and just-in-time delivery ensure components are available for automotive assembly lines.
Custom Extrusion with Inplex
Looking for quality custom extrusion products and services? Inplex is one of the leading custom extrusion services in the US, with over 50 years of experience. We pride ourselves on our ability to put the right talent and technology in place to perform the best possible job for our clients.
We own a 42,000 sq. ft. facility in Naperville, Illinois, that is temperature-controlled and features an environmentally friendly closed-loop water cooling system. If you have specific needs or questions, don’t hesitate to contact us!
Back to Blog