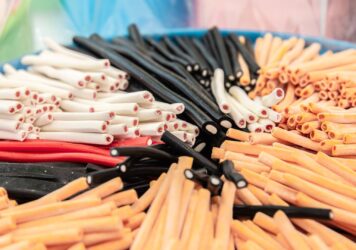
Plastic Extrusion Jacketing
Plastic extrusion coating and jacketing are processes used to apply a protective layer of plastic material onto various substrates or objects. These techniques are widely used in industries such as packaging, electronics, construction, and telecommunications to enhance the performance, durability, and aesthetics of the products.
This article aims to take a closer look at plastic extrusion jacketing specifically. While the processes of extrusion for coating and jacketing are similar, there are some differences that will be apparent in this article.
Plastic Extrusion Jacketing Manufacturing
Material Selection
The choice of plastic material depends on factors such as flexibility, temperature resistance, and environmental exposure. Common materials include polyvinyl chloride (PVC), polyethylene (PE), and polyurethane (PU), among others.
Extrusion
Similar to coating, the plastic resin is melted and homogenized in an extruder.
Application
The molten plastic is extruded through a circular die, which surrounds the object (e.g., cable or wire) to form a continuous protective layer. The object being jacketed is pulled through the die at a controlled speed to ensure consistent thickness and coverage.
Cooling
The jacketed object is cooled to solidify the plastic, using water baths or air cooling systems.
Finishing
The finished product is wound onto reels or cut to specific lengths as needed.
Plastic Extrusion Jacketing Applications
Electrical & Electronics
- Jacketing for electrical cables and wires to provide insulation and protection against environmental factors.
- Used in fiber optic cables to safeguard delicate components.
Telecommunications
Protection of telecommunication cables used in underground and aerial installations.
Construction
Jacketing for plumbing pipes and HVAC ducts to prevent corrosion and damage.
Automotive & Transportation
Protecting wiring harnesses and cables in vehicles from abrasion, moisture, and chemical exposure.
Benefits of Plastic Extrusion Jacketing
- Protection and Durability. Provides a robust protective layer that shields against physical damage, chemicals, and environmental factors.
- Electrical Insulation. Enhances the safety and performance of electrical systems by preventing short circuits and electrical leakage.
- Flexibility and Customization. Can be customized in terms of thickness, color, and material properties to meet specific application requirements.
- Ease of Installation. Facilitates the installation and handling of cables and other components by providing a smooth, uniform surface.
Custom Extrusion with Inplex
Looking for quality custom extrusion products and services? Inplex is one of the leading custom extrusion services in the US, with over 50 years of experience. We pride ourselves on our ability to put the right talent and technology in place to perform the best possible job for our clients.
We own a 42,000 sq. ft. facility in Naperville, Illinois, that is temperature-controlled and features an environmentally friendly closed-loop water cooling system. If you have specific needs or questions, don’t hesitate to contact us!
Back to Blog