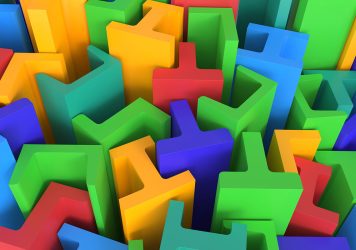
Plastic Extrusion FAQs: Everything You Need To Know
Custom plastic materials and products have taken the manufacturing world by storm. Plastic extrusion applications offer manufacturers a more flexible and durable alternative to metal material. Explore the world of plastic extrusion with leading manufacturer, Inplex, as they offer comprehensive insights into this process. Discover everything you need to know about plastic extrusion FAQs and find answers all in one place.
According to Allied Market Research, the thriving global extruded plastics market witnessed remarkable growth, soaring from $185.6 billion in 2020 to an impressive projected value of $289.2 billion by 2030. This surge can be attributed primarily to the escalating demand for consumer goods, coupled with an upsurge in the building & construction industry. Together, these factors have been the driving force behind the increasing demand for extruded plastics.
Keep reading to learn everything you need to know about common plastic extrusion FAQs. Get the answers to frequently asked questions about plastic extrusion, such as: “Which industries utilize plastic extrusion for their products?” and “What type of plastics can be used in the extrusion process?”.
What Is Plastic Extrusion?
If you have never heard of plastic extrusion before then you are definitely wondering what plastic extrusion is and why is it so common. Plastic extrusion is a process used to create various products, such as the following:
Plastic extrusion methods involve pushing plastic material through a specialized tool called an extruder. It melts and shapes the material into a continuous, fixed, cross-sectional profile.
The extruder tool is divided into four sections, each with its own function:
- The feed zone is where the material is fed into the extruder and prepared.
- The transition zone is where the material is compressed and plasticized.
- The mixing zone is where the material is melted and mixed homogeneously with a special mixing element.
- The metering zone is where the melted material is pushed through the shaping die to be molded into the end product.
Since 1967, Inplex has been a leader in plastic extrusion and custom plastic parts manufacturing. Through custom plastic co-extrusion and normal extrusion processes, we provide our clients with various applications and material selections based on their needs.
Top 5 Frequently Asked Questions About Plastic Extrusion
If you’re curious to learn more about plastic extrusion, here are some answers to the top 5 frequently asked questions about plastic extrusion.
What Types of Plastic Can Be Used in the Extrusion Process?
Choosing the right plastic material for your plastic extrusion project depends on many things such as, how the application will be used, where it will be used, and the project cost constraints.
There are many thermoplastic resins available for use in the plastic extrusion process. A plastic extrusion expert can help you determine which material is best for your custom tubing application. Here are some of the plastic materials available for plastic extrusion.
- Acrylonitrile Butadiene Styrene (ABS)
- Kynar Fluoropolymer
- High Impact Polystyrene (HIPS)
- Nylon
- Polyurethane
- Polycarbonate
- Rigid Vinyl (RPVC)
- Flexible Vinyl (FPVC)
View Inplex’s complete list of plastic materials. Explore the distinctive advantages offered by each plastic material when used for plastic extrusion.
Partnering with Inplex ensures that you will confidently select the perfect plastic material tailored to your project’s specific needs. Whether it’s plastic for outdoor use or indoor applications, navigating the optimal plastic choice has never been easier with our expert guidance at your side.
Which Products Can Be Manufactured Through Plastic Extrusion?
Many household and industrial products can be manufactured through plastic extrusion. It’s a popular tool in many fields, including the automotive, medical, and fuel industries. Common end products include the following:
- Pipes and tubing, including those used in the fuel and medical industries, and outdoor gutter systems
- Tubing for irrigation systems
- Wire and cable insulation and jacketing
- Window and door frames and fittings
- Weatherstripping products, such as draft excluders and rubber products
- Car parts, such as windshield wipers and squeegee blades
- Bottles, straws, bags, sporting equipment, and certain children’s toys
- Highway safety markers
- Outdoor plastic furniture
What Are the Advantages of Using Plastic Extrusion for Manufacturing Products?
Plastic extrusion provides increased durability and flexibility at a lower cost than alternative materials, such as stainless steel and metal. Custom plastic extrusions are also tolerant and resistant to various fuel types, impact types, and heat.
Other advantages of plastic extrusion include the following:
- Decreased waste production
- Constant operation capabilities
- Faster turnaround times
- Improved customizability
With Inplex, you gain access to the expertise in creating custom plastic tubing, available in a diverse array of materials, shapes, and sizes, perfectly suited for a wide spectrum of applications.
Entrusting your needs to a specialized extrusion manufacturer like Inplex allows your organization to create adaptable and tailored plastic tubing products, that meet your unique requirements and applications.
Discover the top extrusion options for your custom extruded plastic tubing projects and applications.
What Factors Affect the Quality and Consistency of Plastic Extruded Products?
A few factors can affect these aspects of plastic extruded products. These factors include:
- Base Material: Some materials, such as TPE, have a higher shrink rate, which can affect tolerance control. Other materials, such as PVC, have a lower shrink rate and a higher tolerance.
- Profile design: More complex profile designs, including those with increased wall thickness and those using hollow areas, tend to have a reduced tolerance.
- Process conditions: The conditions of the surrounding environment, including ambient temperature and humidity, can affect quality and consistency. It’s important to plan ahead for quality control measures.
At Inplex, we have a strong commitment to quality assurance that sets us apart. Our ISO certification stands as a testament to our stability and reliability, making us the preferred choice for major brands. Count on Inplex to deliver excellence, ensuring your utmost satisfaction in every custom plastic extrusion project.
What Industries Commonly Use Plastic Extrusion for Their Products?
Many industries have begun using plastic extrusion processes to manufacture certain products:
- Consumer housewares
- Electrical and utilities
- Highway safety
- Indoor lighting
- Oil and gas
- Outdoor living
- Retailers
- Warehouses- Conveyor roller sleeves & covers
Inplex’s on-site engineering and tooling capabilities bring significant time and cost savings to companies spanning various industries, from Consumer Housewares and Point of Purchase Displays to Lighting, Electrical Utilities, and Highway Safety.
With a comprehensive range of in-house services, including engineering, color mixing, and access to over 100 raw materials running on 10 extrusion lines, we cater to diverse manufacturing needs.
Plastic Extrusion and The Oil and Gas Industry
Several different industries have begun using custom-extruded plastic in their manufacturing processes. For example, Inplex has enhanced the oil and gas industry by creating a plastic extruded application called Injectorplex. Injectorplex is a state-of-the-art engineered tubing that is used to replace stainless steel oil and gas injection tubing.
When compared to its metal counterpart, Injectorplex has many advantages. One advantage is its resistance to the following elements, among others:
- Fuels
- Solvents
- Acids
- Flow (creep)
- H2S
- High temperatures with continued use
Manufacturers who have switched to custom plastics in their daily operations have soared ahead of their competition. Learn more about the best oil and gas injection tubing: Injectorplex. See how Inplex has revolutionized the way gas and oil industries work.
Where to Find Plastic Extrusion Companies Near Me
When searching online for plastic extrusion companies, you might find yourself with a few different results. However, none can compare to Inplex.
Inplex is a privately owned company and leader in plastic extrusion. With more than $15 million in annual sales and operating on three shifts with ten plastic extrusion lines, Inplex is the manufacturer you need. We welcome the opportunity to tackle any challenge and find the perfect solution for your requirements.
Luckily Inplex serves the entire United States market, so it doesn’t matter what state your company is in if you need plastic extrusion. If you’re looking for the best plastic extrusion company near you with experience in the extrusion process and custom extrusion plastics, look no further than Inplex. Let us know what we can do for you today!
Back to Blog