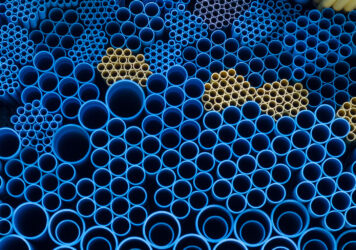
Overcoming Common Challenges in Plastic Extrusion Projects
Plastic extrusion is a widely used manufacturing process that enables the creation of versatile and complex products. From pipes and tubing to custom profiles, this method offers cost-effective solutions across various industries. However, like any manufacturing process, plastic extrusion comes with its own set of challenges.
Understanding and addressing these challenges is critical to ensuring successful project outcomes. Let’s dive in and take a closer look.
Material Selection and Compatibility
One of the most common challenges in plastic extrusion projects is selecting the right material for the application. Different materials have varying properties, such as flexibility, strength, thermal resistance, and chemical compatibility. Choosing the wrong material can result in poor product performance or premature failure.
To overcome this challenge, manufacturers should collaborate closely with material experts and suppliers. Testing materials under real-world conditions and consulting industry standards can ensure the chosen material meets all functional and environmental requirements.
Maintaining Dimensional Accuracy
Dimensional accuracy is crucial in plastic extrusion, as even minor deviations can lead to products that fail to meet specifications. Factors such as temperature fluctuations, uneven cooling, and die wear can impact the precision of the extruded profiles.
Regular equipment maintenance and calibration are essential to maintaining accuracy. Advanced monitoring systems, such as laser measurement tools, can provide real-time feedback, allowing operators to make immediate adjustments. Additionally, consistent process control and quality checks throughout production help ensure that tolerances are met.
Managing Material Flow & Die Design
Achieving uniform material flow is another challenge in plastic extrusion projects. Uneven flow can result in defects such as warping, surface irregularities, or weak spots in the final product. Poor die design or improper temperature settings are often the root causes.
Addressing this issue requires careful attention to die design and manufacturing. Custom-designed dies tailored to the specific material and product geometry can minimize flow issues. Computational fluid dynamics (CFD) simulations can also be employed during the design phase to predict and resolve potential problems before production begins.
Managing Waste & Sustainability
The extrusion process can generate significant waste, particularly during start-up and die changes. Addressing this challenge is vital for cost efficiency and environmental sustainability.
Recycling scrap material and reintroducing it into the production cycle is one effective solution. Additionally, optimizing start-up procedures and conducting thorough pre-production tests can minimize waste generation. Manufacturers can also explore bio-based or recycled materials to align with sustainability goals.
Custom Extrusion with Inplex
Looking for quality custom extrusion products and services? Inplex is one of the leading custom extrusion services in the US, with over 50 years of experience. We pride ourselves on our ability to put the right talent and technology in place to perform the best possible job for our clients.
We own a 42,000 sq. ft. facility in Naperville, Illinois, that is temperature-controlled and features an environmentally friendly closed-loop water cooling system. If you have specific needs or questions, don’t hesitate to contact us!
Back to Blog