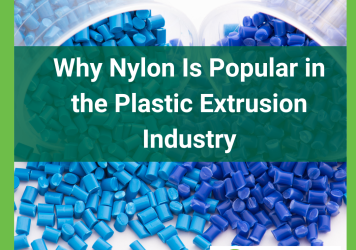
Why Nylon Is Popular in the Plastic Extrusion Industry
First created in 1935 by chemist Wallace Carothers, nylon has expanded from its initial use in stockings and toothbrushes to a host of applications. Now, this chemical-resistant, high-strength plastic is in everything — from clothing to custom plastic profiles — even machine parts. Nylon is popular in the plastic extrusion industry for many reasons. Keep reading to discover the benefits and properties of nylon for your custom plastic extrusion project.
Nylons’ versatility allows for its many uses. One of the most common manufacturing methods for producing nylon goods is plastic extrusion. Useful for producing tubes, sheets, and various other products, plastic extrusion is a cost-effective, efficient mode of fabrication. And the material properties of nylon make it a good match for this process.
This article outlines the chemical structure and material properties of nylon and how these material properties affect nylon’s applications. Learn why it pairs well with plastic extrusion so that you can decide if it’s the right choice for your custom plastic extrusion project.
What Is Nylon?
Although it has several variations, nylon is fundamentally a polyamide thermoplastic. The distinguishing feature of nylon is the presence of a polyamide group, which may connect to other chains to form a longer polymer.
The two most prevalent types of nylon are nylon 6 (PA 6), which has a single backbone chain, and nylon 66 (PA 66), which has two chains linked to one another. Other chemical variations of nylon include:
- Nylon 6/6-6
- Nylon 6/9
- Nylon 6/10
- Nylon 6/12
- Nylon 11
- Nylon 12
The many different variations give nylon unique material properties depending on each chemical structure. For example, nylon 6-6 is more durable than nylon 6, and adding other compounds has a further impact as well. This gives you a variety of unique property options when using nylon for custom plastic extrusion.
What Are the Top Properties of Nylon?
Despite its versatility, nylon plastic generally has several characteristics attuned to its applications. Its soft, lightweight, and breathable feel along with its relative luster make nylon a favorite in the textile industry. Also, some of its other properties make it a good choice for industrial applications.
Some of nylon’s most essential material properties are:
- High strength. With an ultimate tensile yield strength of 186 MPa, extruded nylon 6 is very strong. It can be made even stronger by incorporating glass fibers into the polymer — but this will also make it more brittle, which will help it break more cleanly upon failure. Nylon’s strength allows for a high impact resistance, which makes it favorable for industrial components that experience a high degree of vibration or shock.
- Electrical/thermal insulation. The absence of free electrons in nylon makes it a very poor conductor of electricity. Its uses include serving as an insulator in electrical applications. Nylon also conducts very little heat, making it perfect for products that need to be kept at a constant temperature.
- Chemical resistance. Nylon is resistant to many organic solvents, including hydrocarbons, glycols, and most aldehydes. This makes it a good choice for the oil and gas industry as well as for other environments where products might be exposed to corrosive chemicals.
Another key advantage to nylon is the fact that, like many thermoplastics, it melts all at once rather than progressively. If thermoplastics are reheated after setting — like in a fire — they melt again instead of igniting, which makes them useful as flame-retardant materials. All of these unique properties and benefits make nylon a top plastic extrusion material.
Plastic Extrusion and Nylon: Industries and Applications
With so much to offer, it’s no surprise that nylon has applications in many different industries, especially involving custom plastic extrusion. Some sectors where nylon is used in plastic extrusion are:
- Thermoplastic Resins – one of the most widely used and versatile plastics for this purpose.
- Electronics — where nylon’s insulating properties are used to create circuit board holders, resistors, and other electrical components — all of which are manufactured via plastic extrusion.
- Industrial equipment — where nylon’s high strength is used to make extruded machine parts able to endure high impacts.
- Oil and gas — where nylon’s corrosion resistance helps extruded pipes or tubes stand up to the most caustic environments.
Plastic extrusion, a long-established manufacturing process, can be used to create many different products. It is a very versatile process, which can produce both thin- and thick-walled products, with custom profiles. It can also be used to coat wires or other products with or without adherence.
Because nylon’s thermoplastic properties make it simple to heat and extrude, plastic extrusion is an effective choice for producing nylon products at a low cost.
Frequently Asked Questions About Nylon & Plastic Extrusion
Is Nylon Considered a Polymer?
Yes, nylon is a well-known synthetic polymer. Nylon is a thermoplastic made from petrochemicals and is one of the most widely used and versatile thermoplastic resins.
How Strong is Nylon Plastic?
Extruded nylon can withstand repeated flexing and is available in a range of grades, from flexible to semi-rigid to rigid. Extruded nylon 6 is very strong. As mentioned above nylon has an ultimate tensile yield strength of 186 MPa.
Does Nylon Have a High Heat Deflection Temperature?
Nylon is a plastic material that enjoys a high heat deflection temperature. In fact, nylon has a higher heat deflection temperature than polyurethane, as well as better chemical resistance and higher working pressure. Polyurethane and nylon both provide excellent abrasion resistance, offering protection from oils and fuel.
Is Nylon Crack Resistant?
In terms of crack resistance, nylon takes the cake and serves as something of a standard for industrial applications that require increased heat and chemical resistance. If you need a plastic extrusion material with high crack resistance, nylon is an excellent choice!
Polyurethane vs. Nylon Plastic Extrusion
Nylon and Polyurethane are frequently compared; both have a variety of advantages and disadvantages when compared. Polyurethane and Nylon are two of the most popular materials for custom tubing and plastic extrusion.
Polyurethane is recommended for applications that require a tighter bend radius. Nylon on the other hand can withstand repeated flexing. Which is better: Polyurethane vs. Nylon? This all depends on the project at hand.
As mentioned above nylon has a high deflection temperature, much higher than polyurethane. The material works better with chemicals and withstands a higher working pressure. Polyurethane is the go-to material when used for wire abrasion protection. The material can be melted down and allowed to cool several times over without losing its structural integrity.
Inplex Custom Extruders is here to help determine which material is best for your custom tubing and plastic extrusion project. Contact Inplex and speak with one of our plastic manufacturing experts today. We can assist you in determining the specifications for your next custom plastics project and answer any questions that you might have.
Inplex Offers Top-Rated Nylon Plastic Extrusion
Inplex has an experienced team of engineers well-versed in many different resin types, including nylon. Our state-of-the-art facilities are capable of custom plastic extrusion for even the most complex designs. We carry a wide selection of plastic resins for our clients to choose from.
Inplex is the best place for nylon plastic extrusion. One of our company’s main priorities is quality assurance. Inplex has received an ISO certification which Identifies Inplex to the global market as a stable company with reliable standards. Inplex continues to be a major supplier of custom extruded plastic tubing, belting, and profiles.
Are you seeking nylon plastic extrusion services? Inplex offers in-house engineering and in-house tooling which saves companies time and money. We serve a variety of industries and have customers in industries like Consumer Housewares and Point of Purchase Displays to Lighting, Electrical Utilities, and Highway Safety industries. Inplex offers in-house engineering, color mixing, and over 100 raw materials running on 10 extrusion lines.
Our team can help you decide which plastic manufacturing process is best for your application and which resin would suit it best. Contact us today to see how we can help.
Back to Blog