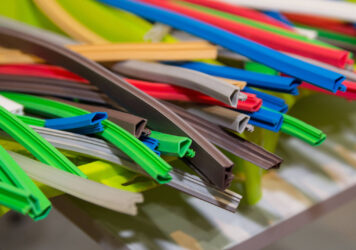
How to Choose the Right Material for Your Project
Selecting the right material for your custom plastic extrusion project involves balancing performance requirements, cost, regulatory needs, and processing considerations. By understanding your application’s demands and collaborating with an experienced extrusion partner, you can choose a material that meets both functional and economic goals.
This guide is intended for those looking at general questions that should be answered before starting a project. Exact material decisions should be made with an expert–based on the general questions this guide will provide.
What are Your Application Requirements?
Consider what the final product will do. Will it be used in a high-stress environment, require flexibility, or need to hold a specific shape? The primary function of the product will significantly influence the material choice.
For example: flexible PVC is ideal for wire insulation, while rigid PVC is better for window profiles.
Also, remember to take into account the operating conditions your product will face. Will it be exposed to extreme temperatures, moisture, UV radiation, chemicals, or wear and tear? These factors help determine the need for materials with specific properties, such as heat resistance or UV protection.
What Material Properties do You Need?
Different plastics offer unique combinations of properties, so it’s important to understand which materials best align with your project’s requirements. These properties should include things like:
- Durability/Strength. For heavy-duty applications or where the product will experience wear and tear, look at solid materials like polycarbonate or acrylonitrile butadiene styrene , which offer high strength and impact resistance.
- Flexibility. If your product needs to bend or be flexible, more malleable materials like polyethylene or thermoplastic elastomers offer the necessary pliability.
- Chemical Resistance. For products that will come into contact with chemicals, consider materials such as polypropylene, fluoropolymers, or others that resist corrosive substances.
- Thermal Stability. If your application requires the product to withstand high or low temperatures, materials like nylon or polypropylene are ideal for their heat resistance. For extreme conditions, you may even consider materials like Teflon.
Do You Have Compliance and/or Safety Requirements?
Knowing if you will run into safety and/or compliance issues is one of the most important things when choosing materials for your project. You need to make sure that any material used in your components passes any regulatory requirements.
In some industries, such as medical or food packaging, materials must meet specific regulatory standards, such as FDA, RoHS, or REACH compliance.For example, in the medical field, medical-grade silicone or PVC may be required to ensure biocompatibility.
For industries where fire safety is a concern (e.g., electronics or building materials), considering using flame-retardant plastics like polyvinyl chloride or polycarbonate is wise.
Do You Have Any Branding Requirements?
Before moving to production you should make sure that any branding requirements are met. Everything from color to shape needs to be in sync with any brand standards.
- Color Matching. If aesthetics are important for your project, such as consumer products or branding applications, choose materials that allow for custom color matching or finishes. Acrylic or ABS are popular for high-quality surface finishes and easy color customization.
- Surface Finish and Texture. Depending on the product’s use, you may need a specific surface texture or gloss level. Some materials, like polystyrene, offer smooth finishes, while others, like polyethylene, can have more matte or textured surfaces.
When choosing any material, make sure it falls within your brands guidelines and quality standards.
Custom Extrusion with Inplex
Looking for quality custom extrusion products and services? Inplex is one of the leading custom extrusion services in the US, with over 50 years of experience. We pride ourselves on our ability to put the right talent and technology in place to perform the best possible job for our clients.
We own a 42,000 sq. ft. facility in Naperville, Illinois, that is temperature-controlled and features an environmentally friendly closed-loop water cooling system. If you have specific needs or questions, don’t hesitate to contact us!
Back to Blog