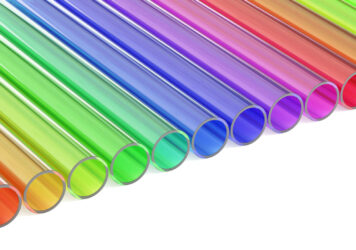
How Plastic Extrusion is Supporting Renewable Energy & Sustainability Efforts
As the world shifts towards more sustainable practices and the demand for renewable energy increases, industries are finding new ways to contribute to environmental goals. One such method is through the use of plastic extrusion, a manufacturing process that plays a significant role in supporting renewable energy and sustainability efforts.
Plastic extrusion involves the continuous shaping of plastic materials into uniform profiles, making it a versatile and essential technology in creating components that enhance energy efficiency, reduce waste, and facilitate the production of renewable energy systems. Let’s take a closer look.
The Process of Plastic Extrusion
Plastic extrusion is a highly efficient process in which plastic material, often in the form of pellets or powder, is melted and forced through a mold to create long shapes of uniform cross-sections. These profiles can be used in a wide range of applications, from construction to automotive and, increasingly, renewable energy technologies. The extrusion process can be customized to produce plastic components of different sizes, shapes, and properties, making it ideal for creating parts that need to withstand specific environmental conditions or contribute to energy-saving designs.
Supporting Renewable Energy Infrastructure
One of the most significant ways plastic extrusion is supporting renewable energy is through the production of components for solar, wind, and hydroelectric power systems. In the solar industry, for example, plastic extrusions are used in the manufacturing of frames for solar panels.
These frames need to be durable, lightweight, and resistant to weathering, all qualities that plastics can offer. Extruded plastic frames allow for easy handling and installation of solar panels, which is vital for large-scale solar projects. Additionally, plastics are resistant to corrosion, unlike metals that can degrade over time, particularly in outdoor environments exposed to moisture and UV radiation.
Energy Sector Solutions
In the wind energy sector, plastic extrusions are also playing an essential role. Plastic profiles are used for components in wind turbine blades, nacelle covers, and even cabling insulation. The lightweight nature of plastic materials helps to reduce the overall weight of these parts, allowing wind turbines to operate more efficiently and with less mechanical stress. Furthermore, the use of extruded plastic components helps reduce the cost of manufacturing wind turbines, making wind energy more affordable and accessible.
Hydropower systems, which harness the energy from flowing water, also benefit from plastic extrusion. Pipes, valves, and fittings used in hydropower plants are often made from plastic, which is resistant to corrosion and wear from water exposure. Plastic extrusions in these applications ensure long-lasting, efficient energy generation while reducing the maintenance costs associated with metal parts that are prone to rust and corrosion in such environments.
Enhancing Energy Efficiency and Reducing Waste
Plastic extrusion also supports sustainability by enabling the production of energy-efficient products. For example, custom extrusions can be used to create insulation materials for buildings, HVAC systems, and pipelines, helping to reduce heat loss and energy consumption.
These insulation materials are vital for improving the energy efficiency of homes, businesses, and industrial facilities. By reducing the amount of energy required to heat or cool spaces, plastic extrusions contribute to a decrease in overall energy demand and, subsequently, a reduction in greenhouse gas emissions.
Furthermore, plastic extrusion is central to the development of recycling technologies that support circular economy initiatives. Extruded plastic products can be made from recycled materials, helping to reduce the consumption of virgin plastic and minimizing plastic waste. The versatility of plastic extrusion means it can be applied to create a wide range of recycled plastic products, from packaging to construction materials, thereby closing the loop on plastic usage and supporting sustainability efforts.
Lightweight Alternatives to Traditional Materials
One of the key sustainability advantages of plastic extrusion is the ability to create lightweight components that reduce energy consumption during transportation. Lightweight materials are essential in various industries, particularly in renewable energy, where transporting heavy materials can result in significant carbon emissions. Extruded plastic parts, such as lightweight piping for fluid transportation or lightweight frames for solar panels, can help minimize the carbon footprint of renewable energy infrastructure projects.
Custom Extrusion with Inplex
Looking for quality custom extrusion products and services? Inplex is one of the leading custom extrusion services in the US, with over 50 years of experience. We pride ourselves on our ability to put the right talent and technology in place to perform the best possible job for our clients.
We own a 42,000 sq. ft. facility in Naperville, Illinois, that is temperature-controlled and features an environmentally friendly closed-loop water cooling system. If you have specific needs or questions, don’t hesitate to contact us!
Back to Blog