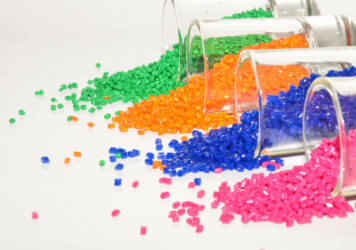
How Does Plastic Tri-Extrusion Work?
Plastic tri-extrusion is an advanced manufacturing process used to create plastic products with three distinct layers. This technique involves simultaneously extruding three different types of plastic materials through a single die, resulting in a single product with three layers.
Plastic tri-extrusion offers several advantages over traditional single-layer extrusion processes. By combining multiple materials in a single product, manufacturers can create composite materials with enhanced properties, such as improved strength, durability, or aesthetics. Tri-extrusion also enables the production of complex profiles with precise layer thickness control, allowing for greater design flexibility and customization.
Applications of plastic tri-extrusion are diverse and include industries such as automotive, construction, packaging, and consumer goods. Common products produced through tri-extrusion include multi-layered pipes and tubing, window profiles, decorative trim, and packaging films.
With its ability to create high-quality, multi-layered products in a single manufacturing step, plastic tri-extrusion continues to be a valuable technology in modern plastics processing. Let’s take a quick look at how the process works.
Material Selection
The first step in plastic tri-extrusion is selecting the appropriate materials for each layer of the product. Different plastics may be chosen based on factors such as desired properties (e.g., strength, flexibility, chemical resistance), appearance (e.g., color, transparency), and intended application.
Extrusion Process
Once the materials are selected, they are fed into separate extruders, which are machines that melt and pressurize the plastic pellets. Each extruder is responsible for one of the three layers of the final product. The molten plastic from each extruder is then fed into a single die assembly.
Die Design
The die assembly is a critical component of the tri-extrusion process. It consists of a specially designed die head with three separate channels or openings, each corresponding to one of the plastic layers. These channels merge within the die to form a single combined flow of molten plastic.
Layer Formation
As the three streams of molten plastic merge inside the die, they are shaped and fused together to form a single continuous profile with three distinct layers. The die is carefully designed to control the flow and thickness of each layer, ensuring uniformity and consistency throughout the extrusion process.
Cooling & Solidification
After exiting the die, the tri-extruded profile passes through a cooling zone, where it is rapidly cooled to solidify the plastic layers. This may involve techniques such as air cooling or water quenching, depending on the specific requirements of the material and product.
Final Processing
Once the tri-extruded profile has solidified, it may undergo additional processing steps such as cutting, trimming, or surface finishing to achieve the desired dimensions and surface characteristics. These steps help prepare the product for further assembly, packaging, or use in the final application.
Custom Extrusion with Inplex
Looking for quality custom extrusion products and services? Inplex is one of the leading custom extrusion services in the US, with over 50 years of experience. We pride ourselves on our ability to put the right talent and technology in place to perform the best possible job for our clients.
We own a 42,000 sq. ft. facility in Naperville, Illinois, that is temperature-controlled and features an environmentally friendly closed-loop water cooling system. If you have specific needs or questions, don’t hesitate to contact us!
Back to Blog