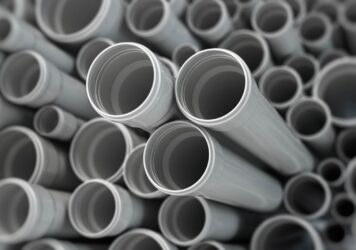
How Custom Plastic Profiles Enhance Product Durability
Custom plastic profiles enhance product durability by allowing for targeted material choices, structural reinforcements, environmental resistance, and functional design. This not only improves product reliability but also helps reduce maintenance and replacement costs over time, making custom extrusions a valuable investment for any product requiring long-lasting performance.
Below are some of the most important ways plastic profiles help enhance product durability.
Material Optimization
Custom plastic profiles allow precise selection of materials, ensuring that the chosen plastic fits the product’s durability requirements. High-performance plastics like polycarbonate and PVC can withstand factors like UV exposure, extreme temperatures, or chemical exposure, which is essential in applications where durability is crucial.
Enhanced Structural Integrity
By tailoring the shape and thickness of plastic profiles, custom extrusion can create parts that resist stress, impact, and wear. This is especially valuable in automotive, construction, and industrial applications where products face constant physical stress. Structural reinforcements, like ribs or thicker walls, can be incorporated to improve impact resistance and strength without adding excessive weight.
Resistance to Environmental Conditions
Products often need to withstand environmental factors like moisture, temperature changes, and sunlight. Custom plastic profiles can be designed to incorporate UV inhibitors, moisture barriers, or specific coatings, making them ideal for outdoor or harsh environments. This enhances their longevity and maintains their functionality even when exposed to challenging conditions.
Design Flexibility for Custom Functionality
Custom profiles enable design elements that are both functional and protective, such as integrated seals, flexible gaskets, or multi-layered profiles. For example, profiles with built-in gaskets or seals help protect products from water or air infiltration, which can lead to corrosion or degradation. Custom designs thus directly contribute to the product’s longevity by reducing potential points of failure.
Reduced Wear & Tear
Custom extrusions allow for smoother finishes and specialized coatings, which minimize friction and wear in moving parts. For example, custom profiles used in sliding or rotating mechanisms can have low-friction materials or finishes added to reduce wear. This prolongs the lifespan of components in high-friction environments, such as machinery and automotive applications.
Custom Extrusion with Inplex
Looking for quality custom extrusion products and services? Inplex is one of the leading custom extrusion services in the US, with over 50 years of experience. We pride ourselves on our ability to put the right talent and technology in place to perform the best possible job for our clients.
We own a 42,000 sq. ft. facility in Naperville, Illinois, that is temperature-controlled and features an environmentally friendly closed-loop water cooling system. If you have specific needs or questions, don’t hesitate to contact us!
Back to Blog