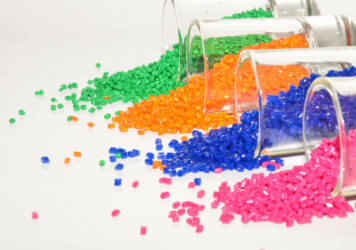
Design Considerations for Custom Plastic Extrusions
Designing custom plastic extrusions involves several key considerations to ensure that the final product meets functional, aesthetic, and manufacturing requirements. Careful consideration of these factors helps ensure that custom plastic extrusions are functional, aesthetically pleasing, and cost-effective.
Let’s take a look at some of the things that need to be considered when designing custom plastic extrusions.
Material Selection
Properties. Choose a plastic material with the appropriate properties such as strength, flexibility, impact resistance, UV stability, and temperature tolerance.
Additives. Consider the need for additives like colorants, fillers, or stabilizers to achieve specific performance characteristics.
Cross-Section Design
Shape and Size. Design the cross-sectional profile to fit the intended application, whether it’s a tube, profile, sheet, or custom shape.
Thickness. Ensure that wall thickness is consistent and appropriate for the product’s strength and flexibility requirements. Avoid abrupt changes in wall thickness, which can lead to weak points.
Design
Complexity. Design the die to accurately produce the desired profile. Complex shapes may require more intricate die designs and careful temperature and pressure control.
Cooling. Plan for effective cooling channels in the die to ensure even cooling and prevent defects such as warping or uneven surfaces.
Manufacturing Constraints
Extruder Capacity. Design with the extruder’s capacity and limitations in mind. Ensure that the profile and dimensions are feasible given the equipment’s capabilities.
Material Flow. Consider how the material flows through the die and adjust the design to minimize issues like flow imbalances or material hang-ups.
Performance
Load-Bearing. Design for the mechanical loads the product will experience. Consider factors like bending, compression, and impact resistance.
Environmental Conditions. Account for environmental factors such as exposure to chemicals, moisture, UV light, and extreme temperatures.
Aesthetics
Surface Finish. Decide on the surface texture and appearance. The extrusion process can achieve various finishes, from smooth to textured.
Color. Choose colors and finishes that match aesthetic requirements and branding.
Post-Processing
Additional Operations. Consider whether the extruded product will need additional post-processing such as cutting, drilling, or assembly.
Ease of Assembly & Use
Integration. Ensure the design allows for easy integration with other components or systems.
Ergonomics. Design with user interaction in mind, especially if the product will be handled or used directly by people.
Cost Efficiency
Material & Production Costs. Optimize the design to balance performance and cost. Consider ways to minimize material waste and streamline the manufacturing process.
Custom Extrusion with Inplex
Looking for quality custom extrusion products and services? Inplex is one of the leading custom extrusion services in the US, with over 50 years of experience. We pride ourselves on our ability to put the right talent and technology in place to perform the best possible job for our clients.
We own a 42,000 sq. ft. facility in Naperville, Illinois, that is temperature-controlled and features an environmentally friendly closed-loop water cooling system. If you have specific needs or questions, don’t hesitate to contact us!
Back to Blog