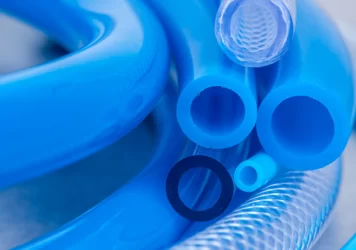
Common Plastic Extrusion Profiles
When it comes to the industrial manufacturing world, it’s hard to miss the key role of plastic extrusion profiles. These custom plastic profiles are much more than just components, but the real game-changers driving innovation and efficiency in a variety of industries. Without plastic extrusion profiles, many of the products we rely on would not be possible, and if they did they would be far more expensive!
At Inplex Custom Extruders, we’re not just a plastic profile manufacturer; we’re pioneers in the custom plastic extrusion field, continually adapting and innovating to meet the dynamic needs of the industry.
This expert plastic extrusion profile guide will walk you through the diverse universe of plastic profile extrusions. Our plastic extrusion experts will provide industry insights and information for those interested in leveraging the benefits of custom plastic extrusion.
What are Plastic Extrusion Profiles?
Plastic extrusion profiles represent an advanced manufacturing process used to create versatile and customized plastic shapes and components for numerous industries. Plastic extrusion is central to producing a wide range of products essential in daily life and specialized applications.
Plastic profiles are created by custom extrusion experts at Inplex to manufacture tailored solutions for our diverse client needs.
What is Plastic Extrusion?
Plastic extrusion is a complex process that results in unique components that can have increased beneficial properties. Far more than other types of standard non-extruded plastics.
Understanding the Plastic Extrusion Process
The plastic extrusion process begins by melting raw plastic material, typically in pellet form, and pushing it through an extruder. During this process, different types of plastics can be fused together to form a final plastic profile that has the combined benefits and characteristics.
The Role of the Die in Custom Plastics Manufacturing
To create the component, or shape needed, a detailed and precise die is needed. Then the molten plastic is subsequently forced through this die, effectively shaping it into the desired profile.
Cooling and Solidifying
The hard part of the custom plastic extrusion process is now over! Post-extrusion, the new custom plastic profile undergoes cooling, typically using water or air, to solidify into its final shape. Once it is fully cooled it is ready to send off to the customer!
Customization in Extrusion
One of the key benefits of plastic extrusion is the ability to leverage heavy customization to the final product. While other materials like steel, iron, or wood are limited, plastics allow for a far greater range of customization.
Plastic Extrusion Offers Design Flexibility
Our plastic extrusion capabilities range from creating simple strips to complex multi-cavity profiles. This unique design flexibility for custom plastic profiles allows us to meet the specific needs of unique industries and create profiles and components that otherwise would not be possible.
Selecting the Right Material for Your Plastic Profile Extrusion
A variety of plastic materials, including PVC, polyethylene, and advanced high-profile plastics, are utilized, each offering unique properties for plastic profile extrusion. Our design and engineering teams will work closely with you to determine what properties are needed in your final product. Then we can create a custom plastic profile that meets all your requirements.
Color and Finish Options
Many clients are looking for custom plastic profiles and other end products like custom plastic tubing that will fit into their design aesthetic or branding. Fortunately, Inplex provides customization in terms of color and finish. This allows our clients to get whatever end look they need while enhancing both functionality and overall aesthetic appeal.
Applications Across Industries
As we mentioned previously, plastic extrusion profiles are key in a variety of industries. Everything from agriculture, and outdoor plastics, to medical devices. Even your homes are full of items that rely on plastic extrusion and custom plastic profiles.
You’d be surprised at the number of consumer household goods using plastic extrusion by Inplex!
Plastic Extrusion Components for Warehouses and Storage Facilities
Inplex has the ability to manufacture custom plastic components for the modern warehouse industry. These custom plastic extrusion components can include conveyor roller sleeves, conveyor roller covers, and other custom plastic parts for your warehouse.
Automotive Sector Use of Custom Plastic Extrusion Profiles
The Automotive industry relies heavily on custom plastic extrusion profiles. These plastic profiles are crucial in manufacturing lightweight yet durable parts for vehicles. Without these custom plastic automobile components, the vehicle’s manufacturing cost would be much higher, and automakers would be limited in the customizability of the parts.
Medical Applications of CustomPlastic Extrusion
Custom plastic extrusion is also common within medical applications. These components are paramount for producing plastic medical tubing and equipment where precision and hygiene are essential.
At Inplex we can create a variety of custom plastic medical tubing to meet your specific needs.
Advancements in Plastic Extrusion Technologies
Plastic extrusion is an industry that continues to innovate and grow. Inplex works hard to make sure that we are at the frontier of custom plastic extrusion and implement the latest technology to deliver superior plastic extrusion profiles.
State-of-the-Art Equipment
We employ advanced extruders and dies for precise and efficient production in plastic extrusion profiles.
Innovative Techniques
Our commitment to staying updated with the latest extrusion methods expands the possibilities of plastic profiles.
Common Plastic Extrusion Profiles
Common plastic extrusion profiles reveal their diverse range of applications, demonstrating the adaptability and versatility of this manufacturing process. Serving as fundamental components across various industries, each profile is meticulously designed to meet specific functional requirements.
Tubing and Pipes
Extensively used in medical, industrial, and residential settings, these profiles showcase the precision and versatility of extrusion plastic, essential for applications requiring sterile, durable, and flexible tubing solutions.
Application Versatility of Custom Plastic Extrusion
The process of custom plastic extrusion enables the creation of unique extruded profiles, tailored to specific project needs, showcasing the capability of plastic extrusion technologies to produce components that are functionally effective and aesthetically pleasing.
The broad spectrum of applications for these common plastic profiles, ranging from everyday consumer products to specialized industrial components, is a testament to their significance in modern industry and everyday life.
Benefits of Common Plastic Profiles
Exploring the benefits of common plastic profiles helps to explain their integral role in various industries. Stemming from the unique properties of plastic extrusion technologies, these benefits include the creation of versatile, durable, and cost-effective components.
- Versatility in Design and Application: The versatility of common plastic profiles, such as profile plastics and plastic extrusion profiles, is one of their primary advantages. They are customizable to meet specific requirements, whether it’s for complex shapes in industrial machinery or aesthetic designs in consumer products.
- Durability and Longevity: Known for their strength and durability, especially when produced using advanced plastic extrusion technologies, plastic profiles resist wear and tear, withstand environmental stressors like UV radiation and moisture, and maintain their integrity over extended periods.
- Cost-Effectiveness: The plastic extrusion process’s efficiency results in cost savings, as it allows for the production of large volumes of profiles quickly and with minimal waste.
- Lightweight Nature: The lightweight nature of these profiles, in comparison to metal counterparts, offers significant benefits in various applications.
- Custom Plastic Extrusion for Specific Needs: Custom plastic extrusion facilitates the creation of profiles meeting specific performance criteria, such as heat resistance, flexibility, or electrical insulation.
- Environmental Resistance: Plastic profiles are known for their excellent resistance to chemicals, moisture, and other environmental factors, making them suitable for use in harsh conditions.
- Aesthetics and Finishing Options: The range of finishing options available for plastic profiles, from various colors to textures, is crucial in applications where aesthetics are as important as functionality.
What are High Profile Plastics?
High-profile plastics are advanced materials, characterized by superior strength, durability, and resistance to extreme conditions, making them essential in industries that demand robust and reliable materials.
- Enhanced Properties: With increased temperature and chemical resistance, high-profile plastics surpass standard extrusion plastic in performance.
- Critical Applications: These plastics are extensively used in demanding sectors like aerospace and automotive, where material integrity under stress is essential.
- Advancements in Extrusion Technology: The development of high-profile plastics is a clear indication of significant advancements in plastic extrusion technologies, showcasing the industry’s innovative capacity.
High-profile plastics represent the forefront of plastic extrusion profiles, meeting the stringent demands of modern, high-stakes applications.
How to Choose the Right Extrusion Plastic
Choosing the right extrusion plastic for plastic extrusion profiles is a crucial decision in the manufacturing process, impacting the performance and suitability of the final product. This selection should be based on a comprehensive understanding of material properties and the specific requirements of the intended application.
- Understand the Application Requirements: The initial step involves defining the plastic profile’s intended purpose, considering factors such as environmental exposure to chemicals, UV light, or extreme temperatures.
- Consider the Material Properties: Different plastics, each with varying attributes like flexibility, strength, and heat resistance, should be evaluated. Profile plastics such as PVC are known for their versatility and durability, making them suitable for a wide range of applications.
- Evaluate Compliance and Standards: It’s essential to ensure that the chosen plastic meets relevant industry standards and compliance requirements, particularly for sensitive applications like food processing or medical equipment.
- Assess the Cost-Effectiveness: Consideration of the cost implications of different plastics is crucial. Some high-performance materials may offer superior properties but come with a higher price tag.
- Seek Expert Advice: Consulting experts like Inplex in plastic extrusion technologies can provide valuable insights, helping to choose the best materials for specific needs, considering both technical and economic aspects.
A detailed approach to this selection process ensures that the chosen plastic material will fulfill its intended purpose, aligning with the overall project objectives.
Best Plastics for Plastic Profiles
Identifying the best plastics for plastic profiles requires understanding the specific needs of the application and the inherent properties of various plastic materials. Some commonly used plastics in plastic extrusion profiles include:
- PVC (Polyvinyl Chloride): PVC’s versatility makes it widely used in various applications, offering a good balance of strength, durability, and cost-effectiveness.
- Polycarbonate: Known for its exceptional clarity and impact resistance, polycarbonate is ideal for applications where transparency and strength are key, such as in safety guards and glazing.
- Polyethylene: Celebrated for its chemical resistance and toughness, polyethylene is used in a wide range of applications, from packaging to heavy-duty industrial components.
- ABS (Acrylonitrile Butadiene Styrene): ABS is a popular choice for profiles requiring a balance of impact resistance, toughness, and aesthetic qualities, commonly used in automotive parts, consumer goods, and piping systems.
Each of these plastics offers unique advantages for plastic extrusion profiles, with the choice largely depending on the specific requirements of the application, such as durability, flexibility, cost, and environmental resistance.
Chose Inplex Custom Extruders for Your Custom Plastic Extrusion Profiles
The plastic extrusion profiles industry is vast and varied, offering solutions for a myriad of applications across different industries. At Inplex Custom Extruders, we are dedicated to harnessing the full potential of these materials, providing our clients with high-quality, customized solutions.
Our expertise in custom plastic extrusion empowers us to create plastic profiles for custom manufacturing, tailoring each solution to meet the unique specifications and design requirements of our client’s projects, thereby ensuring both precision and quality in every product we deliver.
Talk to the experts in plastic extrusion profiles to discuss how Inplex can meet your plastic extrusion needs and take your project to the next level.
Back to Blog