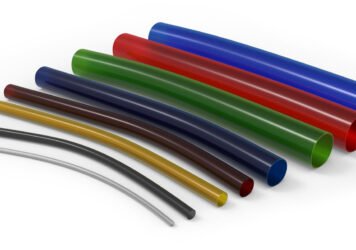
Choosing the Right Plastic Material for Your Project: Key Factors to Consider
A successful custom plastic extrusion project requires careful attention to application requirements, material selection, design, and process optimization. By collaborating closely with an experienced manufacturer and addressing these factors systematically, you can achieve a cost-effective and high-quality product tailored to your specific needs.
When planning a custom plastic extrusion project, several critical factors must be considered to ensure success. These factors span from initial design to final production, and addressing them effectively helps achieve a high-quality product that meets performance and cost expectations.
Let’s take a closer look at some of the most important factors to consider.
Application Requirements
End-Use Functionality
- Determine how the extruded part will be used and what properties are essential (e.g., strength, flexibility, UV resistance).
- Consider environmental factors like temperature, humidity, or exposure to chemicals.
Performance Standards
- Does the product need to meet specific industry regulations or certifications (e.g., FDA, UL, or ASTM standards)?
Material Selection
Plastic Type
Choose the material that aligns with the product’s requirements. Common options include:
- PVC for general durability.
- Polycarbonate for strength and transparency.
- Polyethylene for chemical resistance.
Specialty plastics for unique applications, such as medical-grade or flame-retardant materials.
Additives
Include additives to enhance properties like UV stability, color, or impact resistance.
Design Considerations
Profile Complexity
- Ensure the design is manufacturable within the limitations of extrusion technology.
- Simple shapes (e.g., tubing or flat profiles) are easier to produce than intricate designs with sharp corners or internal cavities.
Dimensional Tolerances
Define realistic tolerances to balance functionality and cost. Tight tolerances may increase production costs.
Wall Thickness
Uniform wall thickness ensures smooth extrusion flow and prevents defects like warping.
Draft Angles and Radius
Adding draft angles or rounded edges can improve material flow and reduce stress during the process.
Quality Assurance
Inspection Protocols
- Establish quality control checks to ensure dimensions, tolerances, and material properties meet specifications.
- Use advanced measuring tools like calipers, laser scanners, or 3D profile analyzers.
Sample Testing
Produce prototypes and conduct testing to validate the design before full-scale production.
Volume and Scalability
Production Volume
- Decide on the quantity required. Larger volumes often justify the cost of custom tooling.
- Small-batch production may require alternative strategies to manage costs.
Scalability
Ensure the extrusion setup can accommodate future production needs or design changes.
Custom Extrusion with Inplex
Looking for quality custom extrusion products and services? Inplex is one of the leading custom extrusion services in the US, with over 50 years of experience. We pride ourselves on our ability to put the right talent and technology in place to perform the best possible job for our clients.
We own a 42,000 sq. ft. facility in Naperville, Illinois, that is temperature-controlled and features an environmentally friendly closed-loop water cooling system. If you have specific needs or questions, don’t hesitate to contact us!
Back to Blog