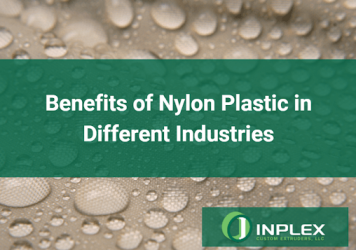
Benefits of Nylon Extruded Plastic in Different Industries
Nylon plastic has become increasingly popular in recent years throughout many industries. Many consumers are unaware of what extruded nylon plastic is and the benefits of using nylon extruded plastic in manufacturing products. There are numerous benefits of nylon plastic in different industries.
In this blog post, we’ll get you up to speed on this incredibly useful and beneficial custom extrusion material. We’ll discuss the history of nylon plastic extrusion, how it differs from another trending plastic (ABS), the advantages that come with nylon plastic extrusion, and how industries are using nylon to supplement their products.
Let’s jump into the benefits of nylon plastic in different industries!
When Did Nylon Plastic Extrusion Begin?
Nylon plastic has been around since 1935 and has since been used to create many traditional products, including toothbrushes, tires, and women’s stockings. It is also the first resin to be engineered — but when did they start extruding nylon?
Around the same time, plastic extrusion became popular and the first successful thermoplastic extrusion process was conducted. The first nylon plant was introduced in 1939. Extruded nylon, also commonly known as extruded polyamide or simply nylon plastic, is available in sheet, rod, and tube formations.
Historically, nylon was often used in wartime and is often referred to as the fiber that won the war. It was available to the public during World War II and played a part in strengthening military products. Nylon was used in parachutes, ropes, tents, and more to create a more durable fabric. It also assisted the military in being able to withstand difficult weather conditions.
The most common plastic nylon extrusion is polyamide 66. Polyamide 66 is a cost-effective and high-performance plastic polymer. PA 6 and PA 12 are two other nylon extrusion types but differ from 66 in mechanical properties and moisture absorption.
How Is Nylon a Plastic?
When nylon first comes to mind, you may tend to think first of nylon fabric or rope. So when Inplex lists nylon as one of their extrusion materials, it’s understandable that many people wonder, “How is nylon a plastic?”
To answer this question, yes, nylon is technically a plastic. Due to how nylon responds to heat, it is considered a thermoplastic. Though it is primarily a type of engineering plastic, it can also be processed into fibers, films, and shapes.
The Nylon Plastic Extrusion Process
The nylon plastic extrusion process is straightforward and involves placing raw resin, or petroleum, into the hopper of an extruder. The hopper pushes the resin through high-temperature barrels.
The high-temperature melts the resin and is transferred to the end of the barrel, where it is transferred from the barrel, through a screen, and then into a feed pipe. In the pipe, the plastic is dyed, cooled, and solidified.
Thanks to this material’s numerous built-in benefits, nylon continues to be widely used for machine parts and other manufactured goods.
Benefits of Using Extruded Nylon Plastic
Now that you know all about the background of nylon plastic and how it came to be, it’s time to learn why you should use extruded nylon plastic. Plastic extruded nylon has several key benefits, including:
- Strength and durability: Nylon is known for its high strength and durability, which makes it an excellent material for a variety of applications. Nylon has a high tensile strength, which means it can withstand much force before breaking, and high impact resistance, which means it can absorb shock without cracking or breaking. These properties make nylon an excellent material for use in applications that require strength and durability, such as gears, bearings, and structural components. Due to its increased ability to withstand wear, particularly on mating parts, nylon plastic extrusion lasts longer than other types of plastics and fibers.
- Chemical resistance: Nylon is resistant to many chemicals, including oils, fuels, and solvents. This makes it useful in environments where exposure to such substances is common such as oil and gas or packaging industries.
- Wear resistance: Nylon is also known for its wear resistance, which means it can withstand abrasion and friction without breaking down or becoming damaged. By being resistant to water absorption, nylon plastic is ideal for use in humid or wet environments.
- Heat resistance: Nylon can withstand high temperatures without melting or degrading, which makes it suitable for use in hot environments.
- Lightweight: Nylon is a lightweight material, which makes it ideal for use in applications where weight is a consideration, such as in the automotive and aerospace industries.
- Soundless: Nylon plastic has a much quieter level of operation. Due to less noise, this makes nylon plastic an advantage in industrial applications such as plastic conveyor roller sleeves and covers.
- Ease of processing: Plastic extruded nylon can be easily molded into complex shapes and parts, which makes it a versatile material for a variety of applications.
- Cost-effective: Nylon is a cost-effective plastic extrusion material compared to many other high-performance plastics, which makes it a popular choice for a range of applications. Plus, as a plastic with great usability and durability, it is cost-effective to maintain, replace, or create nylon plastic.
While nylon plastic extrusion naturally comes with these 8 incredible benefits, Inplex can add one more. While e offer nylon plastic for everyday applications, we also can do custom nylon plastic solutions. Check out our customization services to see how we can help you!
Which Industries Use Nylon Plastic
With that many benefits, it is easy to see why many companies are using nylon plastic extrusion to manufacture their goods. Some of the top contenders and industries using nylon plastic include:
- Electrical: Electronic manufacturers use nylon plastic in coil bodies, case plugs and covers, terminal blocks, cable ties, and more. Nylon is used in electrical and electronic applications due to its electrical insulation properties and ability to withstand high temperatures.
- Oil and Gas: The oil and gas industry uses plastic nylon in a range of applications where strength, durability, chemical resistance, and high-temperature resistance are important. The properties of nylon make it a versatile material that can handle the harsh conditions found in the oil and gas industry. Seals, gaskets, bearings, and piping components are all products that nylon plastic can strengthen.
- Industrial: Overall, nylon plastic is a popular choice in industrial applications where strength, durability, and resistance to chemicals and abrasion are important. Nylon is used in gears and bearings due to its self-lubricating properties, which reduce friction and wear, as well as various machine parts, conveyor belts, washers, and fastenings.
Nylon is also used throughout the food process, fluid handling, and consumer goods industries to create packing and containers to house food and liquids. From gears to coils, whatever nylon plastic product you are looking to produce, Inplex can manufacture it!
Nylon vs. ABS Plastic
ABS plastic is another plastic extrusion material used commonly in both production and manufacturing. Fun fact, a common use of ABS plastic is to make LEGO bricks!
Though ABS and nylon are both types of plastics, they are very different and have different application uses. For example, ABS is less durable and rigid than nylon, so it’s generally recommended to use this type of plastic as a prototype.
Nylon, on the other hand, is more flexible and durable and has better chemical resistance than ABS, making it more appropriate for manufacturing goods and replacing metal in certain materials. When choosing between nylon plastic vs. ABS plastic, nylon is the clear winner.
To learn more about how nylon plastic compares to other inplex materials, check out our latest blogs like “Polyurethane versus Nylon” or “Why Nylon Is Common in the Plastic Extrusion Industry” for more plastic extrusion information!
Inplex Is A Professional Nylon Plastic Extruder
Inplex offers nylon plastic extrusion services and products for many industries, including manufacturing, oil and gas, consumer housewares, electrical, highway safety, plastic, outdoor living, material transport, and more.
Our expert services include the design and engineering of products and materials to tooling, manufacturing, and follow-up services. Inplex offers products ranging from nylon plastic sheets and custom nylon plastic tubing, profiles, plastic coating and jacketing, and nylon plastic customization.
Inplex has over 50 years of experience extruding custom materials, including nylon plastic. Our professionalism ensures that clients are satisfied with their end results. Inplex takes pride in manufacturing and producing high-quality plastics for various industries.
Our experience, material selection, and various applications make us the best choice for a nylon extruder company. Contact us today to get your nylon plastic extrusion order started!
Back to Blog