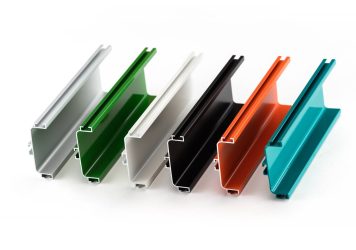
Benefits of Custom Plastic Extrusion Over Standard Plastic Components
Custom plastic extrusion offers a significant edge over standard plastic components in terms of design flexibility, cost efficiency, precision, and material efficiency. For manufacturers looking to optimize their products for performance, durability, and aesthetics, custom extrusion provides the ability to tailor parts exactly to their needs, offering superior results over off-the-shelf alternatives.
Tailoring extruded plastic parts to meet specific design requirements improves functionality, efficiency, and overall product quality. Let’s take a look at some of the key benefits.
Cost Efficiency
Reduced Waste
Custom extrusions are produced exactly to specification, minimizing waste and excess material use. This reduces production costs, as less material is wasted during manufacturing.
Longer Tool Life
Since the tooling is designed specifically for your product, there’s less wear and tear on molds and dies, resulting in lower tooling costs and longer-lasting equipment.
Lower Production Costs
Once the tooling is set, custom extrusion can be highly cost-effective for large production runs. Manufacturers can benefit from economies of scale, particularly when producing large quantities of custom components.
Design Flexibility
The flexibility of designing custom plastic extrusions is one of the key advantages it has over traditional plastic components.
Tailored Shapes and Profiles
Custom plastic extrusion allows for the creation of complex and unique shapes that may not be available with standard components. This flexibility supports innovative product designs, enabling you to produce parts that precisely meet your specifications, whether you need intricate geometries, hollow profiles, or multi-layered designs.
Material Customization
With custom extrusion, you can choose the best materials for your application, including PVC, polyethylene, ABS, and more. You can also modify properties like color, texture, or finish to match your product’s specific needs, something not typically available with standard components.
Consistency
Custom extrusion allows for precise control over dimensions, tolerances, and wall thickness, ensuring that the components meet exact specifications. This is critical for industries like automotive or medical devices, where even slight variations can impact functionality.
The extrusion process also offers consistency from batch to batch, making it easier to maintain quality and uniformity across multiple production runs.
Improved Product Functionality
Enhanced Durability
Custom extruded components can be designed to withstand harsh environments, including extreme temperatures, chemicals, or UV exposure. By selecting the right material and design, you can enhance the lifespan and performance of your product.
Seamless Integration
Custom parts are tailored to fit perfectly with other components, improving the overall assembly process and reducing the need for adjustments. This ensures that the final product works as intended, without requiring modifications or additional parts.
Custom Extrusion with Inplex
Looking for quality custom extrusion products and services? Inplex is one of the leading custom extrusion services in the US, with over 50 years of experience. We pride ourselves on our ability to put the right talent and technology in place to perform the best possible job for our clients.
We own a 42,000 sq. ft. facility in Naperville, Illinois, that is temperature-controlled and features an environmentally friendly closed-loop water cooling system. If you have specific needs or questions, don’t hesitate to contact us!
Back to Blog