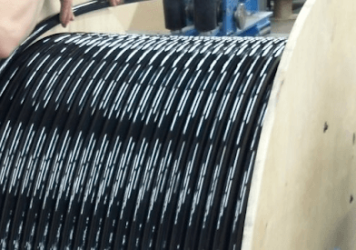
A Step-by-Step Guide to Custom Plastic Extrusion
Selecting the right material for your custom plastic extrusion project is critical to ensuring the success, durability, and performance of the final product. The material choice affects everything from strength and flexibility to resistance to environmental factors.
Let’s take a step-by-step look at how the extrusion process works–from design to manufacturing.
Application Requirements
Consider what the final product will do. Will it be used in a high-stress environment, require flexibility, or need to hold a specific shape? The primary function of the product will significantly influence the material choice.
Take into account the operating conditions the product will face. Will it be exposed to extreme temperatures, moisture, UV radiation, chemicals, or wear and tear? These factors help determine the need for materials with specific properties, such as heat resistance or UV protection.
Assessing Materials
Different plastics offer unique combinations of properties, so it’s important to understand which materials best align with your project’s requirements.
For heavy-duty applications or where the product will experience wear and tear, choose materials like polycarbonate or acrylonitrile butadiene styrene, which offer high strength and impact resistance.
If your product needs to bend or be flexible, materials like polyethylene or thermoplastic elastomers offer the necessary pliability.
For products that will come into contact with chemicals, consider materials such as polypropylene or fluoropolymers, which resist corrosive substances.
And if your application requires the product to withstand high or low temperatures, materials like nylon or polypropylene are ideal for their heat resistance. For extreme conditions, consider materials like Teflon.
Prototyping
Prototyping: Before committing to large-scale production, test the material in a prototype phase. This allows you to evaluate how the material performs in the intended environment and ensure it meets the necessary functionality and durability requirements.
Work with an Experienced Partner
When selecting materials, it’s valuable to work with an experienced plastic extrusion provider. They can guide you based on your specific needs, recommend the best materials, and help optimize the extrusion process for both cost and performance.
Custom Extrusion with Inplex
Looking for quality custom extrusion products and services? Inplex is one of the leading custom extrusion services in the US, with over 50 years of experience. We pride ourselves on our ability to put the right talent and technology in place to perform the best possible job for our clients.
We own a 42,000 sq. ft. facility in Naperville, Illinois, that is temperature-controlled and features an environmentally friendly closed-loop water cooling system. If you have specific needs or questions, don’t hesitate to contact us!
Back to Blog